Las forjas de precisión generalmente se procesan mediante forja en matriz (denominada forja fina) en general o en equipos especiales de forja en matriz que forjan alta precisión de un pequeño proceso de forja nuevo sin corte. Por lo tanto, reemplaza el método de forja tradicional y logra el objetivo de ahorrar materiales, mejorar la productividad de la planta de forja y mejorar las condiciones de trabajo.
Características del proceso de forjado de precisión, las forjas finas se pueden dividir en forja a temperatura ambiente, temperatura media y alta según las diferentes temperaturas de la palanquilla deformada.
La forja fina debe calcularse en palanquilla, al mismo tiempo que los requisitos de precisión y calidad de corte son altos. Debido a la forja cerrada, se debe adoptar menos y ningún método de calentamiento por oxidación. El tocho de forja a temperatura ambiente debe ablandarse (recocerse) antes de forjarse.
El troquel de forja de precisión generalmente usa la combinación de troquel de forja, y tiene dos pasos de preforja (forja inicial) y forja de precisión (forja final) y dos matrices de alimentación, la forja de precisión (forja final) es más alta que la forja dos.
Debido a que la forja de precisión tiene ventajas significativas de ahorro de metal y reduce en gran medida el tiempo de corte, como forjas de engranajes cónicos rectos y engranajes helicoidales con dientes, no es necesario cortar después de la forja, y la parte del cuerpo de la cuchilla de la forja de precisión de la cuchilla no necesita cortar de nuevo
A medida que la forja de precisión fortalece todos los enlaces relevantes en el proceso de forjado en matriz, el costo aumenta. Por lo tanto, la forja de precisión se utiliza generalmente para piezas difíciles de cortar o laboriosas, así como forjas con mayores requisitos de rendimiento, como engranajes, ruedas helicoidales, álabes torcidos y piezas de aviación.
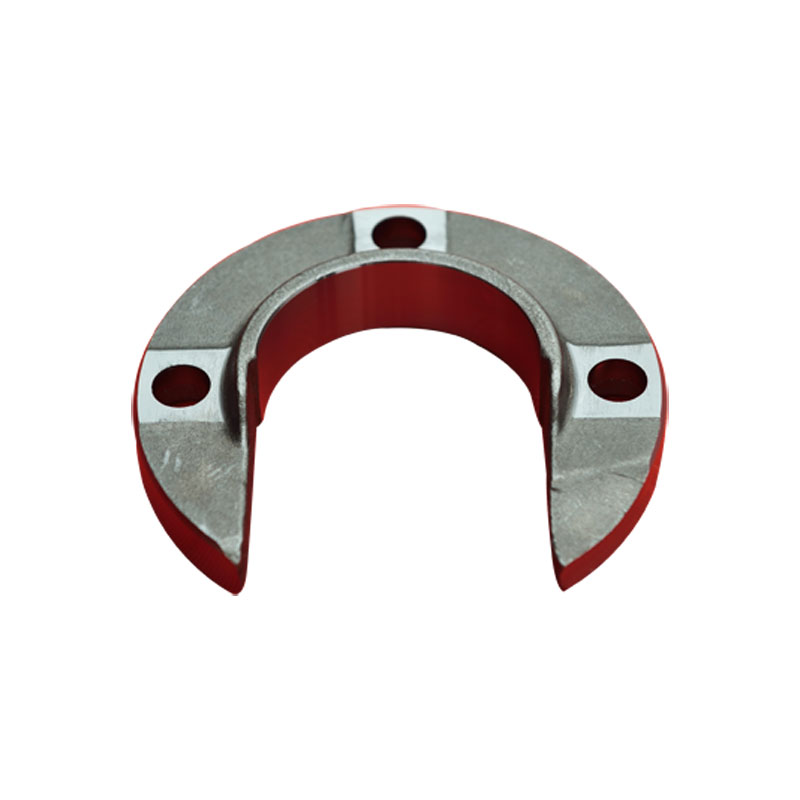